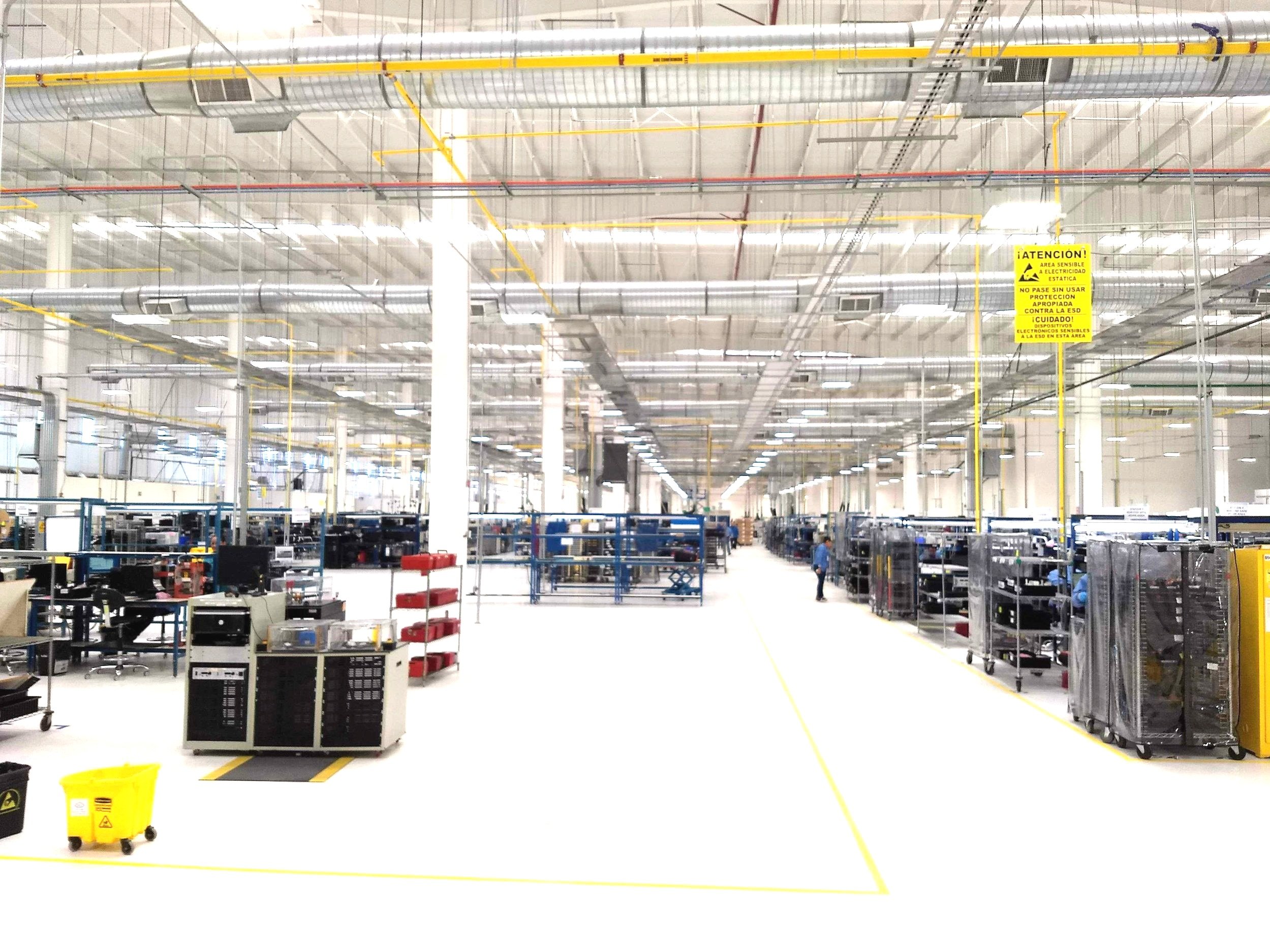
ship it
As product engineers we’re usually focused on getting things through the design and production process and into the hands of end users. As a high priced consultant it’s rare to have the opportunity to see this process from start to finish; usually my team is engaged to kickstart the product development cycle or when trouble arises along the path to production (and we need to fix the problems - fast). The amalgamation of my experience shows how effective I can be at any (and all) steps along the way.
I start with the end in mind
In the early stages developing a handheld, consumer product with internal parts that needed to endure high temperatures (> 300C), a very obvious question arose - what’ll it be made of?! After some research my team found a technical ceramic called alumina. To understand the feasibility of using this material we made a ‘dummy’ part (at that point only a clunky proof-of-concept proto existed) and reached out to manufactures on Alibaba. By engaging potential manufacturers very early in the process we were able to lay the foundation for a product that could confidently be produced.
My teams anticipate problems
With my hands on experience with innumerable products + ideas, I know where problems arise and how they arise - before they arise: thermal problems, production problems from bad assembly, and incorporating difficult to source components to name a few. Because I can anticipate these issues I keep the team’s schedule and budget on the rails - and avoid fires before they start.
We make it right
On the path to production everything matters - especially when the quantities will be in the millions and small changes would result in massive expenses. Things like hinge / snap / button & switch design must be meticulously examined and poured over: tolerance stacks, prototypes with production intent materials, and team design reviews are a must when products are on the fast track to production.
tools for production, too
I can easily slip between different roles and design a variety of different things. While I primarily design things to be produced, sometimes it’s the way things are produced that needs ingenuitive thought. One assignment that our team was on presented an interesting (and critical) problem: how can you quickly and non-destructively remove a handlebar grip from a scooter on a fast paced production line? After giving serious consideration to a flippant suggestion (Tom H: “hmm…perhaps you could suck it off?”) I invented a tool to do exactly that. In only 5 weeks (and 2 iterations) I was training technicians in Mexico to use the vacuum tool that I fabricated in our shop for fast and effective grip removal.